Pulse tools:
Pulse tools are high-capacity, efficiency assembly tools. These tools are designed for high-volume manufacturing environments and use air pressure to produce significant torque. Pulse nut-runners (pulse tools) are tools that have a discontinuous motor. Rather than a single continuous blast, they apply torque in small increments. Since they provide force in quick bursts of pressure, they protect operators by avoiding the high reaction forces created by standard air tools. However, in order to do so, they must be properly used and cared for. You must put in some effort if you want your tool to work for you. We’ve put together a guide on how to use and maintain pulse torque tools to help owners and operators understand the best practices.
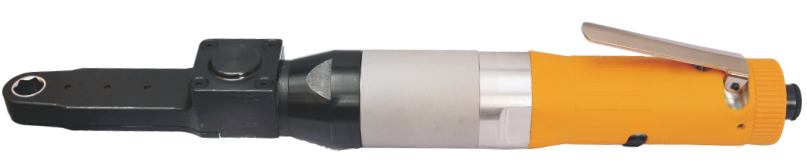
How Does A Pulse Tool Work?
A pulse torque tool has the speed of an impact wrench and the repeatability of a clutch-based torque tool. The pulse unit is a sealed chamber that is filled with a formulated hydraulic fluid and contains precision-machined elements. The hydraulic fluid absorbs the majority of the vibration from the fastening phase, which is a key benefit of the pulse tool design. Torque reaction is almost non-existent since torque is applied intermittently in fast short bursts. The fluid inside the spinning chamber is pushed by pulse blades with a specially built precision roller, creating hydraulic pressure that generates torque. The pulse tools are activated by air force, which spins the anvil and creates resistance against the fastener.
Primary reason to choose a Safe Ergonomic Pulse Tool
– Durability
– Power & speed
– Low noise decibels
– Minimal vibration
– Low torque reaction
Best Practices for Pulse Tool Use
Oil pulse tools are designed for long service life and durability. Controlling torque is important for businesses to ensure that the performance, safety, and durability of their products are not compromised. A three-cent fastener that hasn’t been properly tightened can cause catastrophic or latent failures. Improperly torqued fasteners can vibrate loose, and excessive torque can strip threaded fasteners. Many companies are increasingly focusing on a high-quality pulse tool to ensure that sufficient torque is applied and that gauge standards consistent with the ISO 9001 Quality Standard are met.
“Know your tool” is the first rule of the tool usage. The operator must be trained in certain basic principles, such as:
- Basic operation and the intended use of the device, in order to properly use a high torque pulse tool.
- Recognition of common issues including premature shut-off, no shut off, low torque, incomplete rounds, inconsistent torque output and low RPMs.
- The correct air hose connection, disconnection and storage procedures.
- Tool damage recognition, including leaks, loosened connections, cracks, and teeth.
- A regular inspection is necessary, both the soft and hard parts of your pulse tool.
- Your pulse tool should be recognized for maintenance if it’s not in good working condition.
- It is essential to maintain the right quality and quantity of oil for the continued operation of a pulse tool.